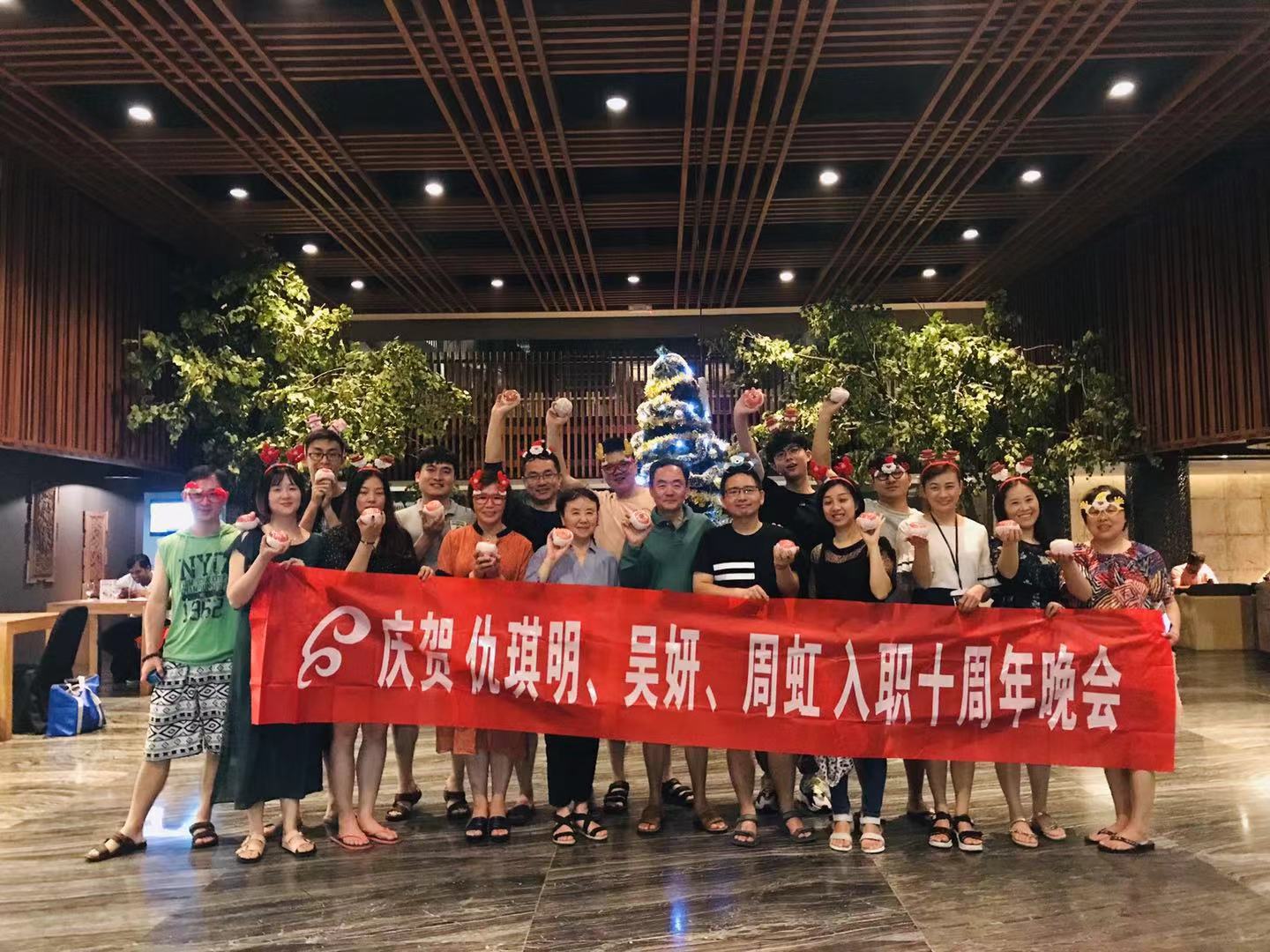
Mr. Terry
Leave a messageMr. Terry
Leave a message
Researchers at the Fraunhofer Institute for Reliability and Structural Durability in Germany have developed a lightweight tie rod for mid-size cars. The component is made of carbon fiber and has a 35% reduction in weight compared to steel counterparts. In addition, the researchers plan to integrate multiple functions into the tie rods to achieve higher fault tolerance and comfort. To this end, the researchers used a structural health monitoring system (SHM) and a semi-active system to reduce the propagation of solid sound.
For designers, how to ensure that the fiber composite structure is designed to meet fiber characteristics and to ensure that the components are safe and reliable in use is a huge challenge.
Compared to metals, fiber composites behave more complexly under load, so it is not possible to simply replace the metal structure with a fiber composite. Considering the processing technology and the anisotropy of the fiber composite, different approaches are required for different materials at the time of design. Fiber composites must be designed to meet the characteristics of the fiber, so these reinforcing fibers must be aligned in the direction of the load.
Tension of the lever when the load is "turning to the brakes"
One of the challenges faced by researchers at Damsdart is how to make the manufacture of fiber composite components suitable for mass production. The results show that organic slabs using a matrix of thermoplastic materials are particularly suitable for the fabrication of large and planar components. The material is injection molded in the mold according to the shape of the member. For material-based thermoset plastic matrix systems, it is conceivable to process the components using a resin transfer molding process.
LBF researchers emphasize that designing stable and reliable automotive chassis components requires consideration of all the factors involved in the operation of the components. The load design of the component is based on the set of loads acquired by the measuring wheel in one driving cycle. These sets of values are converted into external forces to which the individual components are subjected. Critical driving behavior is derived from driving behavior, and these thresholds are used as hypothetical loads. According to the further explanation of the researchers, different driving behaviors caused intricate multi-axial load conditions in the region with the highest load, which needs to be evaluated in consideration of driving safety.
Optimized coating structure
The researchers conducted a pilot study on the materials used, constructed a material model basis based on the research results, and evaluated the lifespan accordingly. Using digital simulation methods, the researchers identified various load areas, and the fiber reinforcement in the structure needed to change according to the load direction. Studies have shown that in order to support local fiber reinforcement, the braided layer needs to be coated. In order to optimally adapt the braid to the stress load, the layup structure is digitally optimized based on the local fiber direction.
Light reveals damage
High load conditions can damage the structure of the component and shorten the life of the component, such as a traffic accident or overload on a poor road surface. With structural health monitoring systems consisting of fiber optic sensors and optical cables, researchers can monitor these damaged areas online. When a crack is created in the monitored area of the component and the damage is aggravated, the deformation of the area is exacerbated, and the fiber optic sensor captures these changes. When the set minimum value is exceeded, the driver will get a corresponding alarm display.
Damping vibration in fiber composites
Lightweight structures that are subject to dynamic loads are prone to vibration and typically use a device such as a damper to reduce vibration. The disadvantage of using this method is that it requires extra weight and space. To this end, researchers at the Fraunhofer LBF Institute integrated the damper with a piezoelectric transducer that uses passive component wiring. The principle is to use the induction line and the converter together as a resonant circuit, thus replacing the mechanical damper. In order to achieve high efficiency, LBF researchers have adopted this semi-active system in the development of fiber composite components, so that they can produce components with low weight and good damping performance.
Ningbo Ram Electric Material Ltd.
Business Type:Manufacturer , Trade Company
Product Range:Ceramic Fiber Blankets , Heating Equipment , Mica
Products/Service:Mica Sheet , Mica Heating Film , Mica Tape , Mica Tube , Mica Heating Element , Mica Paper
Certificate:ISO9001 , CE , EMC , RoHS , TUV , UL , VDE
Company Address:Room 1001-A, No. 312 Alley 645 Renmin Road, Jiangbei, Ningbo, Zhejiang, China, Ningbo, Zhejiang, China